Rack and stack: with 10 traps to build and hang in one day, there's no time to lose!
The team create portable acoustic treatment for a composer who has plans to move house.
This month's Studio SOS features the studio of Hilgrove Kenrick, a professional TV and film composer who recently wrote a series of articles in Sound On Sound about producing music for picture (see SOS December 2005-March 2006). While writing the series, Hilgrove decided to move his studio from a room in his house into a new double-garage construction and asked Hugh and I if we'd take a look to advise on acoustic treatment. The twist was that he ideally needed a portable approach, as there was a chance he'd be moving house within the next year or two.
We came up with an idea for some wall-mounted hanging panels and thought that this rather construction-intensive project would make an interesting Studio SOS — which is why mid-December saw us at Hilgrove's home with a car full of electric saws, nail-guns and cordless screwdrivers. Hilgrove had already bought in all the raw materials we'd specified for the job, other than the foam, which was generously provided by Auralex, via their UK distributor Audio Agency.
The Task Ahead
Hilgrove's studio space is large enough to make most people envious — roughly 23 x 21 feet, and 10 feet high — but other than 10mm Noisestop Solutions rubber matting (the type made from recycled car tyres) that Hilgrove had fitted to the floor, all we had to work with was four painted plaster walls. At the back of the studio are two wooden garage doors separated by a masonry pillar. To save doing anything too permanent there, we suggested that Hilgrove buy a couple of large, thick duvets to hang in the garage-door recesses. He could later hang some thick curtains across the entire back wall, to improve its appearance, if necessary. If it turned out that more bass absorption was required, Hilgrove could easily hang barrier mat directly behind the duvets, to form a limp mass-absorber (providing it was allowed to hang freely). This damped wall would be useful for recording vocals, as the singer could stand with their back to it. Barrier mat is quite expensive to buy in quantity and the shipping cost can add another 50 percent to the bill, but at least it can be taken down and re-used in a future studio. We decided to leave this part of the job for later, as it didn't involve any serious DIY work, to which Hilgrove has a self-confessed allergy!
Diagram showing the basic construction of a single trap.DIY allergy nothwithstanding, Hilgrove had already sealed the spaces around the doors, and the walls of the garage are triple-skinned. As his house is reasonably secluded, soundproofing isn't a major concern. Hilgrove has a background in IT, so he's put all the noisy computing gear in a separate machine room with backup UPS power supplies and hooked it up to his keyboard, monitors and Sony digital mixer via cable extenders and MADI looms (running to RME interfaces), which makes his control room quiet enough for serious recording work.
Our plan for the day was to build 10 sound-absorbing traps to hang on the front and side walls, then to fit two further pieces of acoustic foam to the ceiling, to kill reflections from above the mixing position. We could simply have used foam panels on the walls, but their low-end absorption is only worthwhile if they are very thick or spaced from the wall. They can also be difficult to fix up temporarily in a neat and professional way, although Auralex do have some Velcro fixings that work adequately on smooth, painted walls. As Hilgrove was also concerned about aesthetics, we decided to build something more substantial, based on a 125mm-deep wooden frame with 600 x 1200mm internal dimensions. This would exactly accommodate a piece of rigid rockwool cavity-wall insulation slab (30mm thick in this case, but deeper slabs would have been even better, had they been locally available), on top of which would be fixed a sheet of Auralex wedge-profile foam.
Paul makes a start cutting pine planks for the frames of the traps.
Hugh glues and screws the corners of the frames.
Wooden batten is fitted to the inside of the frames to help position the rockwool and foam correctly.
Fitting the rockwool slabs into the frames.
The foam panels go on top of the rockwool, secured with spray adhesive.The idea was that the rockwool/foam layers would be at the front of the frame, leaving a decent air-gap behind to help improve the low-end absorption. It also left space to add a sheet of freely-hanging barrier mat behind the rockwool, which we fitted to the two traps that we angled across the front corners of the room. As the type of rockwool slab we used is more dense than foam, it provides better absorption than using foam alone and it is also relatively cheap, which is another reason for taking this approach. The foam panel on the front would do its share of absorbing, as usual, and give a tidy, professional appearance to the finished units. Slotted wall-hanging plates fixed to the back would make each trap easy to fix to the wall using just a couple of screws each, and would also allow the panels to be lifted down without the need to undo the screws.
Making The Traps
When we first encoountered the room almost empty, the reverberation was impressive — but certainly not appropriate in a control room! To make matters worse, all three room dimensions are quite closely related, so prominent standing waves would be a potential problem, although we knew that the wooden garage doors should let a lot of low-end pass directly through to the outside world, which would help. As mentioned earlier, sound leakage is not an issue, fortunately, as there are no close neighbours.
The 10 traps we made helped enormously to tame the reverb and seemed to improve the bottom end to a useful extent, but from the outset we realised that a large area of absorption (duvets!) on the back wall would be a vital component, as the wall was all bare wood and plaster. It might also prove necessary to extend the front corner traps and possibly add more corner trapping on the wall/ceiling boundaries. Real Traps Mini Traps, for example, could be a practical way to trap the wall/ceiling corners, as they are easy to put up and take down if you move house. Essentially you can never have too much bass trapping, and it is easy to add more in stages until the optimum balance has been found. Hilgrove could add these components later as necessary: our intention on that day was to make the room usable for composing and mixing.
To make the frames for our traps, we cut two long sides and two short sides from planks of planed pine timber (using 15mm thick, 125mm wide, 2.4m pine planks), then glued and screwed the corners. No serious cabinet-making skills are required here. You just have to remember that it is the inside dimensions that are important, as the rockwool and foam fit inside the frame. To secure the rockwool slab, we then fitted 20mm wooden batten around the inside of the frame, set back from the front edge by 35mm, so that when the 30mm rockwool was fitted it would sit 5mm behind the front of the frame. This meant that when the Auralex foam was glued to the front of the rockwool, it would be recessed into the frame very slightly, leaving the edges looking clean and tidy.
Having 90mm of air-space behind the rockwool makes a significant improvement to the low-frequency absorption of the trap, and while the wooden frames of the trap are acoustically reflective, we felt they could add a little useful scattering. Traps of this type can be even more effective if you cut holes in the edges to let sound into the back more easily, but as we had to build 10 in a day, we didn't have the time!
We used a couple of wood offcuts to make up some 35mm spacers, upon which we could rest the internal battens as we glued and pinned them in place. This ensured that we got the battens in the right place and avoided the need for measuring every time we fitted a new length. As we had a relatively short space of time in which to finish the construction, we needed to set up an efficient production line, with me sawing and nailing, Hugh drilling and screwdriving and Hilgrove making endless coffee, accompanied by clinically dangerous quantities of chocolate Hob Nobs. Hilgrove also played a few Pink Floyd albums over his studio monitors to keep us motivated.
Hilgrove's studio space before the team started work...
Hilgrove decided to leave the pine frames unfinished, so we just gave them a light sanding prior to fitting the rockwool and foam. However, I have since built similar structures for my own studio and found a suitable water-based satin-finish varnish (from Wickes) that is very easy to apply and also dries quickly.
We found that the simplest way to fix the rockwool into place was to apply a solvent-free 'Look, there aren't any nails, honest guv' type of adhesive via mastic gun to the frontmost edge of the batten (see photo above), then simply push the rockwool into place. As explained earlier, the frame size was decided to ensure that the rockwool slab was an 'interference fit', so the glue didn't have to do much anyway. Auralex's own spray adhesive was used to fix the foam to the face of the rockwool and we applied it to both surfaces prior to bringing them together. It stuck very positively and also looked very neat, but we had to tuck the edges into the frame as we worked, as the foam panel was just slightly larger than the rockwool slab. If you do get the spray adhesive on a visible section of foam or other surface, we discovered that you can usually remove it by dabbing at it with the sticky side of a piece of gaffa tape — as long as you notice it before the glue sets.
Fitting The Traps
Hilgrove had power trunking running along the front and one side wall of his studio, so we simply stood the traps on top of this, marked the wall through the keyhole slot in the hanging plates, then drilled the necessary holes using a masonry bit and a hammer drill. Plastic plugs were hammered into the holes to take the screws, in the usual way. Two of the traps were fitted across the front corners of the room to give more low-end absorption, so we used scraps of wood cut at 45 degrees to fix the keyhole plates at the correct angle. Filling the space behind these corner traps with more loose rockwool would improve their low-end absorption further, but we settled on fitting a piece of barrier mat behind each, as described earlier, to act as limp-membrane absorbers, as these are effective at low frequencies. In a room of this size, such a small area of absorber could only be of limited help, but it certainly wouldn't do any harm.
We hung three of the absorbers on each side wall, two in the front corners and two behind the monitors. The two foam panels we had left over were fixed to the ceiling, using a light dash of spray adhesive. We hope it will be possible to remove them at a later date without damaging them beyond the point where they can be re-used.
The picture-hanging plates used to mount the traps on the walls, so that they can easily be lifted down.
From Hilgrove's listening position, we had all the 'mirror points' covered, but the amount of bass trapping required was still undetermined. However, once the panels had been hung, the acoustics of the room dried up very noticeably and the stereo imaging improved significantly.
Studio SOS: The Return
A few weeks later, we returned to Hilgrove's room, to check on progress and to hang two thick, 13.5-tog, hollow-fibre duvets in the garage-door recesses. (While duck-down is good for sleeping under, it tends to settle to the bottom of the duvet, which is why we went for hollow-fibre duvets, which keep their shape.) Standard kingsize duvets fitted perfectly into the recesses, and we tacked them in place in the door frames using large-headed nails. The duvets dried up the sound to a useful degree.
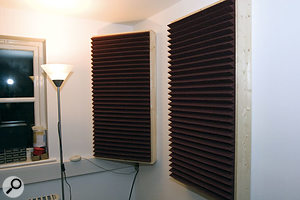
With the 10 traps, the ceiling foam panels and the two duvets the room was surprisingly well behaved, and although more bass trapping would undoubtedly be a good thing, the garage door, room doors and windows contributed to the natural bass trapping of the structure, so there were no really hot or dead bass notes evident.
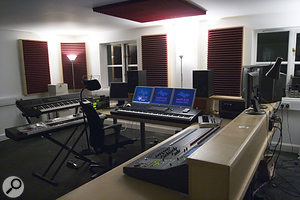
As an experiment, Hugh and I held up a large rug at the back of the room, to see if it would function as a limp-membrane absorber to remove more bass energy. It was surprising how strongly the bass vibrations in the material could be felt, meaning that the rug was indeed drawing energy from the sound field. The bass was slightly but audibly tightened up when we held the rug in place, so we suggested to Hilgrove that he might want to try hanging a couple of rubber-backed rugs in the garage door recesses to provide further bass trapping, and to look nicer than the bare duvets — although I gather Spiderman duvet covers were being considered...
To avoid reflecting mid-range energy back into the room, the rugs should really be hung behind the duvets, but given the distance to the rear walls it probably wouldn't make much of a subjective difference if the rugs were in front, and they'd certainly look nicer than exposed duvet. Our impromptu test with the rug didn't seem to affect the mid-range tonality at the monitoring position.
Hilgrove had brought in a soft sofa, which he positioned at the back of the room. This is always a good idea, as large soft furnishings (and the clients who sit on them!) provide a little extra free trapping.
A return visit enabled Hugh and Paul to hang duvets in the recesses of the wooden garage doors, to further improve the room's acoustics.After a final trial of the room, using the theme music from Batman Begins (which has monstrous bass end) as a test source, we were generally very happy with how much of an improvement we'd brought about for so little outlay. However, there were still some little jobs for Hilgrove to do to optimise his studio, so we left him with a 'to do' list.
We had noticed that the cavity under the closed-back monitor shelf of Hilgrove's work desk seemed to be acting as a resonator, which had the effect of reducing definition towards the low end of the spectrum, so we suggested relocating his Mackie HR824 speakers onto suitably high rigid stands behind the desk, then either filling the offending cavity with foam or other absorbing material, or otherwise removing the shelf completely. As the monitor shelf was directly behind Hilgrove's computer screens, the space below it couldn't be used as practical storage space anyway.
Taking the speakers off the desk would almost certainly tighten up the low-end performance of the HR824s. I had already reset the switches on the back of the monitors to full bass extension and half-space room loading, which seemed to work best for their current position and should be even more appropriate when the speakers are moved to stands a little closer to the wall.
The wall behind the monitors has two windows in it that Hilgrove didn't want to block, so slatted vertical blinds should ideally be fitted to these, to help deflect and scatter reflections. Setting the blinds half-open usually works well. There were also two noticeably untreated side sections of wall left just behind the frontmost side-wall absorption panels, due to the presence of a door in one wall. This door leads to Hilgrove's machine room, which houses the impressive rack of computers that he needs for his extensive use of Gigasampler, running Vienna Symphonic Library and other libraries, for classical compositions. We suggested that Hilgrove buy a couple of panels of matching Auralex foam and fix these directly to the door and to the facing wall, to maintain symmetry. This would improve the sound, particularly the stereo imaging, further back in the room where his clients tend to sit.
Hilgrove's Comments
"When I left the big smoke for a life of creative peace and quiet in the countryside, I hadn't realised I'd end up within 20 miles of the gods of the Studio SOS, Hugh and Paul! I was also lucky enough to have Peter and the team at Total Audio Solutions close by, to advise on MADI and remote extenders, so that I could pile all my noisy PCs, network gear and I/O in the server room, leaving my studio free of extraneous noise.
"The studio room ended up very nearly square — a big no-no — but the builders managed to 'find' another inch or two of width at the last minute. The room previously sounded like an oversized bathroom, but now that the acoustic traps are in place the listening experience is very nearly perfect. I rarely have to record live instruments, so the space will be used primarily for tracking and editing, but having the capability to record live if I need to is most welcome.
"After our second meeting I bought two speaker stands for the Mackies and ditched the overbridge from the desk. Thus I now have space for even more TFT screens and can load the bass as much as I need without the desk resonating its way through the floor.
"Ironically, although everything was done with 'pick up and go' portability in mind, I now like it so much that I'm content to stay!"