Even in today’s computer‑based studios, a patchbay can change your life. We help you choose the right one.
With so much of what we do today carried out ‘in the box’, the humble patchbay is growing rarer outside of professional studios. It’s understandable: many of us now don’t use mixing desks, we use a fraction of the outboard gear we once did, and audio interfaces can now offer enough connectivity that dedicating inputs and outputs to different hardware devices — so they can be accessed directly from your DAW — is possible for all of us.
But patchbays remain very useful. They come into their own whenever there’s a disparity between the numbers of sources and destinations, and they’re also helpful when you want to establish a default signal path that you’ll only need to change from time to time. And they save you having to scrabble around in the dark, under a desk or at the back of a rack! In this article, I’ll take you through the essentials of planning and setting up a patchbay. I’ll also consider some of the possibilities and benefits of using them in a modern project studio.
Essentials
Choosing and configuring a patchbay might seem daunting to anyone who’s not done it before, given the various physical formats and the notion that ‘normalling’ might be complicated. But a patchbay is actually really simple: it’s nothing more than a manual routing matrix. You insert patch cables in sockets on the front, to route signals between the different devices you’ve connected at the rear. A complete studio installation might involve several separate patchbays, but each unit typically comprises two rows of sockets. Usually, sources (equipment outputs) are presented along the top row, and destinations (equipment inputs) are on the bottom row. But this is not an absolute rule: if a situation requires a different arrangement just make sure it’s clearly identified so that everyone can see what’s going on.
The professional Bantam (pictured) and larger B‑gauge plugs are rounded at the end, unlike the consumer TRS jacks most of us are now more familiar with. They’re also a much more robust option, so can be good if you plan on doing lots of patching regularly.For patching balanced analogue audio, professional studios have traditionally employed B‑gauge or ‘longframe’ patchbays. This extremely robust design was developed for manual telephone exchanges, and uses a distinctive ‘PO316’ quarter‑inch (6.35mm) brass plug with three contacts (tip, ring and sleeve). It’s easily distinguishable from the more common but less robust A‑gauge TRS jack (ie. headphone jack) by its small‑diameter rounded tip. Professional‑quality longframe patchbays are expensive, though, and usually have to be professionally hand‑wired into the studio installation.
Where space is at a premium, notably when the setup involves a large‑format console and lots of analogue hardware, a reduced‑scale alternative is often employed: the TT (Tiny Telephone) or Bantam format. The TT/Bantam plugs share the PO316 design but are smaller in diameter (4.4mm). TT patchbays aren’t quite as robust as B‑gauge types but still more so than A‑gauge jacks, and double the number of sockets can be squeezed into a given rack space. Some TT/Bantam patchbays require professional wiring, but others are available pre‑wired with multi‑pin connectors at the rear (such as AES59 D‑subs) to make installation neater and more practical. Again, they can be expensive.
Most amateur or semi‑pro project studios, therefore, tend to use A‑gauge patchbays, which employ the domestic quarter‑inch ‘headphone’ TRS plugs. Given the typically much lighter use in a semi‑pro context this less robust format isn’t usually problematic, and it’s often more convenient, too, as most A‑gauge patchbays also have A‑gauge sockets at the rear, for simple plug‑and‑play installation/reconfiguration. There are also variants with D‑subs or solder pads for hand‑wiring of the rear connections. Some A‑gauge models also include a solder‑free means of reconfiguring the input/output pairs... and that brings me neatly on to that mysterious word, ‘normalling’.
Normalling
Obviously, the point of a patchbay is that any source can be routed to any destination using a patch cord (sometimes called a ‘double‑ender’). But it’s also intended that you can set up semi‑permanent routing: a default routing setup that requires no patch cords. This is what ‘normalling’ is, and it just means that the ‘normal’ routing, with no patch cords inserted, is for the socket in the upper row to be connected to the socket directly below it. Simple!
Switching contacts on each socket make normalling possible. These are ‘normally closed’ (‘nc’), meaning they’ll pass signal when nothing is plugged into the socket. Inserting a plug forces these contacts apart, breaking the connection; they’re sometimes known as ‘break contacts’. There are different ways in which these break contacts can be wired between the two sockets, to make possible two different forms of normalling, each of which has pros and cons.
If there is no connection at all between the upper and lower sockets, you have a third configuration, typically described as a Thru, in which the upper and lower sockets are unlinked and carry completely unrelated signals.
The ‘half‑normalled’ arrangement is the most commonly used one.
The commonest and by far the most useful configuration is ‘half‑normalling’: the signal going to the top (output) socket is also connected directly to the break contacts of the lower (input) socket, so the output signal is always present on the top socket, whatever’s plugged in. This means you can use the output socket as a ‘listen’ to eavesdrop on the output without disturbing the normalled signal path. It can also be used to provide a passive split or ‘mult’ of the output signal, while the source is still passed to the normalled socket below. Plugging a substitute signal into the bottom (input) socket breaks the signal feed from the output socket (hence the term ‘break jack’) and replaces it with the new signal delivered by the patch cord. Stereo inputs on mixers and effects units often use the same arrangement, with the left‑channel input half‑normalled across to the right channel’s input socket. A single mono input is thus automatically routed to both sides of the stereo channel.
A second form of normalling, often offered by configurable patchbays, is variously called ‘single normalling’, ‘full normalling’ or simply ‘normalled’. The output signal is connected to the output socket in the same way, but the signal passed to the lower (input) socket’s break contacts comes from the upper (output) socket’s break contacts. With nothing plugged in, the output signal is routed to the corresponding input, as before, and a source can be over‑plugged into the lower input socket exactly as before. But when a plug is inserted into the upper (output) socket the break‑contacts open, interrupting the signal flow to the lower socket. The output signal from the upper socket is sent only to the patch cord, for routing elsewhere, and the lower (input) socket loses its normalled input feed.
Full normalling, on the other hand, is only normally used in specific situations, such as when patching gear that’s particularly fussy about impedances.
Eavesdropping or splitting/multing of the output is thus not possible, so full normalling is typically employed only where a particular output must not be routed to more than one destination at a time (for example, with devices that are fussy about impedances), or if the normalled input should be muted when its usual source is routed elsewhere.
Whichever form of normalling you opt for, professional B‑gauge and TT/Bantam patchbays usually involve soldering wires between the appropriate socket terminals on the rear. Normalling on most A‑type patchbays, on the other hand, is generally user‑configurable for each pair of sockets, whether by flipping switches on the top (as on, for example, Behringer’s unbalanced PX2000 and balanced PX3000) or the front (as on the Samson S‑Patch), by swapping around reversible cards for each set of linked sockets, or building solder ‘bridges’ across pads on the circuit board. There are pros and cons to each method, in terms of reliability and convenience of reconfiguration. But unless the studio is completely re‑engineered on a regular basis, there should be no need to change normalling arrangements once the installation is complete.
What Should I Connect To A Patchbay?
With all that in mind, what gear might you want to hook up to your patchbay and how? The obvious candidates are things like an audio interface’s line inputs and outputs, outboard processor and effects units’ I/O, any external A‑D/D‑A converter analogue connections, the line outputs and any dedicated line inputs of external mic preamps, auxiliary inputs to monitor controllers, tie‑lines between other rooms or equipment bays, and that kind of thing. I’ll consider these options in more detail below.
Spare sockets on your patchbay can be put to good use. For example, you can easily wire up polarity inverters, pads and mults (parallel outputs) for convenient access.
Unless tracking drum kits or live bands, most project studios now tend to record only one or two sources at a time, yet have a large array of sources to record: various keyboards, mic preamp choices, guitar and bass amp DIs, and so on. Yet most interfaces have a relatively small number of input connections, so a lot of re‑plugging is typically required. With a patchbay, all of the sources are made easily accessible, ready to be plugged into any of your interface’s inputs as required — and with the most‑used sources normalled, no plugging is needed to get up and running. Not only does this approach avoid scrabbling around the back of an interface, it also protects the interface’s sockets by greatly reducing the number of times things have to be connected and disconnected from them. Instead, all the daily ‘wear and tear’ is transferred to the patchbay, which is specifically designed for that task.
A lot of us like to use analogue outboard signal processors with our DAW, either when recording or when mixing or mastering. I’m thinking of bus compressors or other dynamics processors, mastering EQs, effects units or whatever. Using these outboard processors with our software means connecting them to line inputs and outputs on the interface, but as most interfaces only have a few line connections it’s not generally practical to have all outboard connected all the time. The benefit of a patchbay in this kind of situation is that it facilitates quick and easy connection of different outboard devices across the limited spare line I/O of a DAW interface.
In this kind of situation one particular device (a ‘go‑to’ mic preamp, for example) might be used much more frequently than others, so it could make sense to configure that unit with normalled connections to the interface I/O. It might also be the case that you want to chain several units together, with the output of one unit routinely sent to the input of another, such as when forming a custom ‘recording channel’ from separate preamp, EQ and compressor devices; that’s another obvious candidate for normalling. Of course, the beauty of a patchbay is that any and all of these normalled connections can be ‘over‑plugged’ to substitute a different device in the signal path, or to create a different processing order. And all from the comfort of your studio chair.
Spare A Thought
In the ‘thru’ configuration, the upper and lower jacks aren’t connected at all, unless you patch them together with a cord.
Whatever you attach to your patchbay(s), it’s rare that your gear will have exactly the same number of I/O as the patchbay, and it’s worth considering whether you can put any spare sockets on the patchbay to good use. For example, if you’re setting up an A‑type patchbay, you could use spare sockets in a Thru configuration to provide easy remote access to any inaccessible headphone connections that are tucked away at the back of equipment.
Another option is a polarity inverter, which can be achieved simply by making up a short custom cable with the tip and ring contacts swapped at one end: with this link cable connected between the rear sockets of a Thru pair, a signal source connected to the corresponding socket on the front of the patchbay will come out of the other socket in the opposite polarity. This can be useful for Mid‑Sides conversions or for checking signal polarity if a mixer or interface lacks a polarity switch.
A lot of mixers and guitar pedals use the half‑normalling arrangement for the left and right inputs, allowing mono sources to feed both channels.Yet another useful option is to link several rear sockets together to create a Mult or Parallel strip at the front of the patchbay, providing a convenient means of routing one source to several different destinations. And one more might be to wire up a ‘ground‑breaker’ pair, where only the tip and ring contacts are linked, thus providing a handy facility to break ground loops. This sort of thing can save you time and frustration, as you’ll never misplace and have to hunt around for that special cable again!
Lower Latency?
Believe it or not, when working with outboard gear a patchbay can also be useful in reducing latency! A bold claim, I know, but bear with me. I’ve come across some installations in which a large interface is used specifically to allow multiple outboard units to be connected all the time, so that each unit could be accessed individually from within the DAW at the click of the mouse. While this can be a useful way of working in some situations, there are drawbacks.
A patchbay can also be useful in reducing latency! A bold claim, I know...
For example, if the outboard processors are employed in a chain, the signal path necessarily involves multiple A‑D and D‑A conversions as it weaves in and out of the interface and outboard. And the longer the chain, the greater the latency from conversion delays. In contrast, with a patchbay, an identical chain of outboard gear can be plugged together entirely in the analogue domain, so that only one set of converters is required for the start and end of that chain. Hence reduced latency!
What To Avoid
Just as important is what you don’t connect to your patchbay! I strongly advise against patching mic signals on a regular patchbay (see the 'Microphone Patchbays' box). Although it’s technically possible, I’d also advise against using a standard patchbay to route digital audio or control signals, such as S/PDIF or AES3, word clock, MIDI, RS422, DMX and that kind of thing. There are far better alternatives for those sorts of connections.
In professional studios, specialist forms of patchbay are used, such as those from Ghielmetti, or fibre‑optic patches. In the project‑studio world it’s usually more cost‑effective and practical to build custom patch panels using universal D‑type connectors, allowing connections to be made using any combination of XLR, BNC, TRS, RCA‑phono, DIN, Toslink, RJ45, USB, 3.5mm and so on. Putting these on a separate bay reduces the risk of patching things together that don’t play nicely!
As with mic inputs, it’s a good plan to put things like digital clocking and audio signals, and MIDI, on a different type of bay. The D‑series format allows you to build panels with different connectors in a modular way.
Plan For Success!
It’s very easy to over‑complicate a patchbay with connections that will never be used, to omit connections that later prove vital, to set up normalled connections that turn out not to be the best default configuration at all, and to put devices you often want to connect together far apart. So the key to a successful patchbay installation is careful planning. I always start by setting out on paper what connections I require, where each connection will appear on the patchbay, which pairs of connections will be normalled, and in what way. It usually takes several revisions before I arrive at the ideal solution ready for installation, but it saves a lot of time and hassle in the long run, particularly if wiring up a large professional patchbay.
It makes sense to try and keep all of the signal levels in the same format: usually that means balanced and at a nominal professional line‑level (+4dBu). If you do need to mix and match balanced and unbalanced, or pro and instrument levels, then I’d suggest that you try and keep each group apart, in different zones on the patchbay. This will minimise crosstalk and the potential for confusion (see the 'Balanced & Unbalanced' box for more).
Of course, some devices have more inputs than outputs, or vice versa, which complicates the usual ‘input/output pair’ arrangement on your patchbay. For example, some mic preamps have only a mic input (which, as I’ve said, you should not bring out on your patchbay) and a line output. And lots of dynamics processors have side‑chain inputs and/or stereo link sockets. The preamps’ outputs can be organised as simple Thru connections or be normalled to interface inputs easily enough, and grouped together on the patchbay. For things like key/side‑chain inputs, I tend to group those all together in a separate area of the patchbay, as they’re less frequently used and this makes laying out the business end of the patchbay easier.
Overall, then, a patchbay can bring a range of practical and worthwhile benefits to a studio, greatly improving flexibility and operational convenience. The hardware involved isn’t onerously expensive, installation can be plug‑and‑play simple, and this approach is an easy way of growing your studio’s capabilities and versatility without the expense and upheaval of a new interface with a high I/O count.
Microphone Patchbays
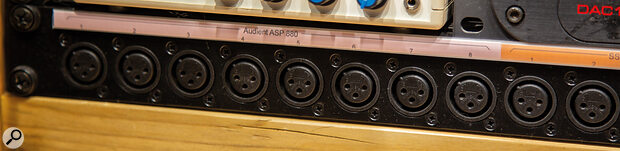
Regardless of the type of patchbay, the action of plugging or unplugging a jack plug inherently causes momentary short circuits between the ‘wrong’ plug and socket contacts. Ordinarily that’s not a problem, as there is negligible DC voltage on standard balanced audio lines. However, if there’s a chance of phantom power being present on the lines being plugged, these shorts can generate very big voltage spikes. If the channel were faded up at the time, these spikes would manifest as loud ‘splats’, which have been known to damage loudspeakers and, even more worryingly, destroy preamp input and microphone output circuitry! A much safer option for microphone patching is to use dedicated XLR patch panels. Sadly, there are no normalling facilities between sockets on these, but that’s not usually a problem for most applications.
And before someone writes in to ‘correct’ me, yes, I know it’s possible to patch mics on standard patchbays, and that there are countless examples of studios where that is done. But it is only a safe practice if phantom power is turned off at the time, or if other technical arrangements are made to isolate phantom power completely from the patchbay. The problems are that the latter is prohibitively expensive and potentially degrades the mic signal quality, while the former is a tragedy waiting to happen; sooner or later someone will inevitably forget to switch phantom off before patching.
A dedicated XLR panel for all microphone patching really is a much better solution. In practice, the studio mic lines would be brought up to male XLRs on the panel, and the inputs to the mic preamps (either on the interface or on outboard units) on female XLRs. Depending on the numbers involved these could be arrayed across a single row of 12 or 16 XLRs on the panel, or on two rows, with outputs on the top row and inputs on the bottom, as in a conventional patchbay. Patching is then achieved with short XLR‑XLR cables, and any ‘hot‑plugging’ at least has the benefit of not risking short‑circuited connections. (I’ll leave the debate about the safety or otherwise of hot‑plugging for a different article!)
Balanced & Unbalanced
If all equipment connections are balanced and at the same nominal signal level, patchbays are very easy to install and use. But things can get complicated very quickly when unbalanced equipment is involved, and ground loops can cause problems. Addressing all the ramifications and potential solutions would make an article in itself but, in my experience, the best starting point is to make (or have made) bespoke TS‑TRS cables for unbalanced devices. These should be wired so that the unbalanced end’s signal (tip) is wired to the tip contact at the patchbay TRS plug, and the unbalanced ground (sleeve) connects only to the ring contact at the patchbay. This minimises the risks of creating ground loops, and is an effective workaround in the majority of situations.
Another, more expensive, solution is to balance some or all of the unbalanced connections. This can be achieved with line‑isolating transformers between the unbalanced equipment and the patchbay, or active balanced/unbalanced converters (the type intended to connect domestic equipment in professional installations). The latter can be particularly helpful when working with instruments or effects pedals, since they also deal with the differences between pro and instrument signal levels.